Please refer to the equipment description, instrument panel pointer display and the annotation instructions under each knob when operating the vacuum coating machine.
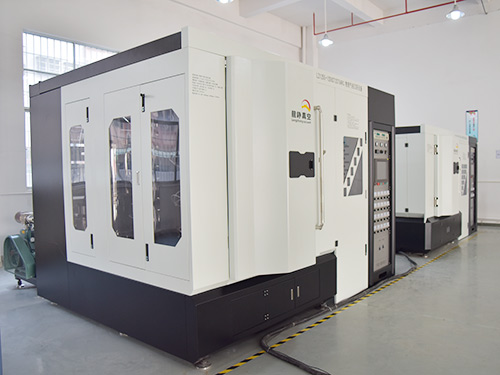
① Check whether the operation control switch of vacuum coating machine is in the "off" position.
② Turn on the main power switch and power the equipment.
③ Low pressure valve pulled out. Open the charging valve, and when the air flow is not heard, start the bell rising valve and the bell cover rises.
④ Install the tungsten screw heater. The PVDF film and aluminum cover plate are fixed on the rotating disk. Put the aluminum wire in the spiral heater. Clean all parts of the bell cover to ensure that there is no impurity.
⑤ Lower the bell cover.
⑥ Start the vacuum pumping mechanical pump.
⑦ Turn on the power supply of the composite vacuum meter (model of the composite vacuum meter: fzh-1a).
a. The left-hand knob "1" is turned clockwise to the heating position pointing to the 2-section.
b. The pointer in the low vacuum gauge "2" moves clockwise. When the pointer moves to 110mA, the left-hand knob "1" rotates to the measurement position pointing to the 2 section.
⑧ When the pointer in the low vacuum gauge "2" moves clockwise again to 6.7pa, the low pressure valve pushes in. At this time, the left-hand knob "1" rotates to the measurement position pointing to the 1 section.
⑨ The vacuum coating machine opens the cooling water, starts the diffusion pump, and heats for 40min.
⑩ Low pressure valve pulled out. Repeat the operation procedure of ⑦ once: turn the lower left knob "1" to the measurement position pointing to Section 2. The pointer in the low vacuum gauge "2" moves clockwise, and when the pointer moves to 6.7pa, open the high-pressure valve (the valve rod rotates clockwise).
⑪ When the pointer in "2" of the low vacuum gauge moves to 0.1pA on the right, turn on the gauge tube filament switch.
a. The transmitting and zero point measuring button "9" is rotated to the launching position.
b. The lower left knob "1" is rotated to the measurement position pointing to the 1 section.
⑫ Rotate the emission adjusting button "4" so that the pointer in the high pressure vacuum gauge "5" points to 5.
⑬ The transmission, zero point and measuring knob "9" are rotated to the zero point position.
⑭ Rotate the zero adjustment button "10" to make the pointer in the high pressure vacuum gauge "5" point to the 0 position.
⑮ The transmission, zero point and measuring knob "9" are rotated to the measuring position.
⑯ Rotate the standard adjusting button "3" to point the pointer in the high pressure vacuum gauge "5" to 10.
⑰ Rotate the "multiplier" switch button "8" to point to 10-12. When the pointer in the high pressure vacuum gauge "5" moves more than 1 anticlockwise, then turn the "multiplier" switch knob "8" to point to 10-3.
⑱ When the pointer in the high pressure vacuum gauge "5" moves more than 6.7pa counter clockwise, turn on the rotary button switch of the workpiece, and the PVDF film of the plated part in the bell cover will rotate.
⑲ Turn on the evaporation button switch. Insert the current plug into the distribution hole of evaporation electrode (1, 2, 3 and 4 holes are provided, and any hole can be inserted).
⑳ Rotate the right hand wheel of the pressure regulator on the right side, and slowly rotate the pressure boost.
a. The color change of the heating temperature of tungsten spiral heater was observed from the mirror window.
b. When the color of the tungsten spiral heater turns yellow orange and the aluminum wire starts to melt, operate the baffle button on the left hand to remove the baffle above the tungsten screw.
c. All the aluminum wires melted and evaporated, and the baffle plate returned to its original position.
d. Rotate the right hand pressure regulator hand to return to zero position. The first steaming work is completed.
21. if you want to steam plating again (to increase the thickness of the metal layer of the electrode): pull the current tap out and insert it into another electrode distribution hole. Repeat the operation.
22. turn off the switch of gauge filament. Close the high pressure valve (turn the handle counterclockwise). Turn off the workpiece rotation. Turn off evaporation. Rotate the mechanical pump knob to the position pointing to the diffusion pump.
23. pull out the low pressure valve. The bell cover is inflated. Inflate for a while, when there is no air. Sound, bell cover.
24. add aluminum wire into tungsten spiral heater. PVDF film is replaced by the other side downward (the original aluminum film is coated with an upward layer). Fasten to the rotating disc.
25. clock cover. Turn on the mechanical pump.
a. The lower left knob "1" is rotated to the measurement position pointing to the 2-section.
b. When the pointer in the low pressure vacuum gauge "2" moves clockwise to 6.7pa, the low-pressure valve is pushed in.
c. The lower left knob "1" is rotated to the measurement position pointing to the 1 section.
d. When the pointer in the low pressure vacuum gauge "2" moves clockwise to 6.7pa, open the high-pressure valve. The knob "1" is rotated to the measurement position pointing to the 2-section.
e. When the pointer in the low pressure vacuum gauge "2" moves clockwise to 0.1pA, turn on the gauge tube filament.
f. Repeat from ⑰ to.
26. after PVDF film is evaporated and plated, close the gauge filament, high pressure valve, mechanical pump and diffusion pump in sequence. Pull the low pressure valve out. The bell cover is inflated and the bell cover is raised after the inflation is completed. Take out the workpiece and clean the bell cover.
a. Lower the bell cover.
b. Start the mechanical pump, pump for 3-5min, and stop the mechanical pump.
c. Turn off the main power supply switch.
d. Turn off the cooling water after 1 hour. All operations are complete.
27. in normal production, if there is a sudden power failure, the high vacuum measurement shall be cut off immediately, the gauge tube filament shall be closed, and the high-pressure valve and low-pressure valve shall be pulled out. After the call, first let the mechanical pump start up for 3-5min, and then transfer to normal production.