How to measure the coating adhesion of coating equipment? The binding force of coating refers to the adhesion ability between coating and the coated substrate surface, that is, the degree of difficulty to peel the coating from the substrate. The harder it is to peel, the better the binding force of the coating. There are three methods used in industry to measure the binding force of coating, which are scratch method, indentation method and ball mark method.
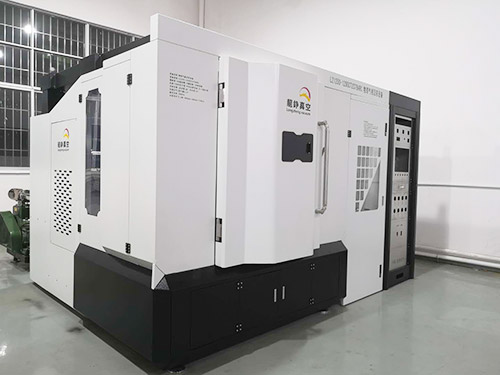
1. Scratch method
Scratch method is a "quantitative" standard test method to measure the adhesion strength and failure mode of coating substrate. A diamond ball needle is used to continuously stroke on the coating surface, and the load is gradually increased on the needle. When the coating is completely scratched or the coating appears obvious peeling off, the loading force is the adhesion force of the coating, expressed in Newton n.
ASTM c1624-05 is applicable to the measurement of adhesion of hard ceramic coatings deposited on ceramic or metal substrates (Vickers hardness higher than 5gpa, thickness ≤ 30um) at room temperature. The simple expression is to mark LC1, LC2 and even LC3 points by observing the scratch image under the microscope, and calculate the applied load at the position where these points appear.
Generally, LC1 means that the scratch edge begins to crack, which indicates that the coating begins to fail. LC2 means that the scratch begins to peel off, which indicates that the coating has completely failed. Generally, we use LC2 to define the adhesion of the coating. At present, this standard is mostly used in the world.
The national standard JB / t8554-1997 is a scratch test method used to measure the adhesion between film and substrate in China. It is used to determine the failure point of coating, that is, the adhesion of coating, by detecting the sound signal at the moment when the coating is scratched. Because the sound is very small, it is difficult for people's hearing to feel it accurately. Generally, a sensor that can accept weak sound is installed between the tested object and the needle, and then the signal is amplified. Generally, the load corresponding to a peak value of the sound spectrum on the sound signal curve is used as the value of the membrane substrate adhesion force.
Because the acoustic signal is greatly affected by the environment, many units still use the method of using optical microscope to observe the scratch track, and determine the binding force of the film substrate by determining the LC2 value. Generally, the price of scratch instruments is more expensive. In China, scratch instruments are more than 100000 yuan, so small enterprises rarely buy them. Generally, large enterprises, schools or research institutes buy scratch instruments.
2. Indentation method
Indentation test is a "qualitative" method to measure the film substrate adhesion force. The diamond indenter of Rockwell hardness tester is used to punch a pit on the designated position of the sample. Due to the deformation of the sample substrate at the pit, the corresponding stress between the substrate and the coating is generated, which may make the coating around the pit fall off. Different testing methods are used for different materials.
For the steel matrix, HRC method is used, and the test pressure load is 150kgf; For the matrix with high hardness, such as cemented carbide, HRA method is used, and the test pressure load is 60kgf. The morphology of the pits was observed under the microscope and compared with the standard to determine whether the adhesion of the coating was qualified. Hf1-hf4 are qualified, hf5-hf6 are unqualified. Most coating companies use this method to test the film substrate adhesion.
3. Ball mark method
The ball mark method is also a "qualitative" method to measure the film substrate adhesion force. It uses a certain diameter of steel ball to grind on the surface of the coating to wear through the coating, leaving a round (when the coating surface is flat) or oval (when the coating surface is cylindrical) dent on the coating and the substrate.
The grinding time should be well controlled, and the depth of the pit must exceed the thickness of the coating. In addition, because the coating is very hard, it is difficult to wear through the coating directly, so when grinding, some diamond powder (particle size is less than 7um) should be coated on the grinding area of the steel ball, and alcohol should be sprayed to dilute the diamond powder and lubricate during grinding.
When the pit is magnified 50-100 times under the microscope, there is a decomposition line between the coating and the substrate. Observe the shape of the dividing line to judge whether the adhesion between the coating and the substrate is good or not. If the boundary line is very clear and neat, the adhesion of the coating is good. If the canine teeth of the boundary line are staggered or there are faults, the adhesion of the coating is not good.